LVK Series Torsional Coupling
The LVK Series is designed for direct coupled equipment. The LVK Series coupling is highly torsionally compliant, allowing the engine to drive a large inertia load safely away from damaging torsional resonance or critical speeds. The coupling selection should be verified with a Torsional Vibration Analysis of the system.
- Designed for direct mounting on SAE J620 and metric flywheels
- Element bonded to flywheel mounting plate and LK style hub housing
- Available in high temp rubber (HTR) or EPDM
- Nominal torque: up to 5,800 in-lb (655 Nm)
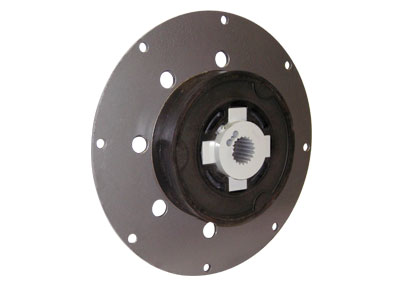
LVK Series Torsional Coupling Additional Resources
Element Features:
- 50 & 60 Durometer (Shore A scale) available
- -40° to 194° F temperature range
- Available in SAE J620 6.5 through 14 Flywheel sizes (some metric sizes available upon request)
- Blind assembly, no lubrication
- Material available in HTR and EPDM
Hub Features:
- High quality powdered-metal construction
- Splined hubs available with L-LOC clamping system
- Engagement Dogs are slightly crowned to avoid edge pressure due to misalignment
- Available in bore with keyway and spline connections
Typical Applications:
- Compressors, centrifugal pumps, hydraulic pumps, and generator sets
Lovejoy’s LF product line supports both standard style elements (above left) and the S-Style elements (above right). The standard style elements bolt to the cylindrical (center) hub and the flywheel, flywheel adapter, or flange hub. The S-Style utilizes bolts which look like dowel pins and are designed for “blind” installations, where the axial bolts may not be accessible for tightening during the installation process. One application would be inside a bellhousing when all the components are assembled and the bolts cannot be reached. The S-Style bolts also accommodate a small amount of end float when necessary to prevent unnecessary axial stress on the element. When looking to replace elements, please note the difference in the axial holes. The standard elements have stepped holes to accommodate the cap screws (above left) which are used to mount the element. The S-Style elements have straight holes (above right) to accommodate the S-Style pins.
The focus of any coupling is the flexible elements, or the “working component”. The element must effectively absorb the shock loads, misalignment forces, and torsional vibrations, under a variety of environmental conditions. The following materials are used to accommodate the different conditions and environments where the couplings are used.
High Temperature Rubber (HTR)
There are two different rubber element materials available, High Temperature Rubber (HTR) and Neoprene (CR). Both elements are torsionally soft andare placed into compression during assembly. Rubber under compressioncan carry up to 5 times the amount of torque as non-compressed elements. The elements effectively accommodate shock, misalignment, and vibration plus minimize harmful radial and axial forces on the connected equipment. Neoprene (CR) is used in environments that are hostile to High Temperature Rubber (HTR).
Available Durometer Hardness : 50, 60, 70, 75 (Shore A scale)
Operating Temperature Range: HTR: -40° to 194° F; CR: -40° to 175° F
Maximum Angular Misalignment: Up to 3°
Hytrel®
Elements made of DuPont’s Hytrel® elastomer compound are torsionally much stiffer than natural rubber (20 times stiffer) and were developed for combustion engine / hydraulic pump applications. Hytrel® elements have 20% greater torque capacity as compared to rubber elements. The torsionally stiff Hytrel® element moves the harmful vibration resonance frequency above the operating RPM range. The element design also reduces harmful radial and axial reactionary forces.
Operating Temperature Range: -60° to 250° F
Maximum Angular Misalignment: 0.25°
Zytel®
Elements made of DuPont’s highly stressable Zytel® elastomeric compound have excellent chemical compatibility and corrosion resistance. The element composition is 3-times stiffer then Hytrel® elements. Zytel® elements exhibit less than 1° wind up at normal torque and zero backlash. Most suited for applications where heat, moisture, high torque / high speed, and corrosion resistance are critical factors in the coupling selection.
Operating Temperature Range: -40° to 300° F
Maximum Angular Misalignment: 1°
Please download Torsional coupling catalog for performance data.
For other Torsional Couplings: see Torsional Couplings
Or, for other coupling types: see Coupling Preselection Guide