The function of a coupling is to connect driving and driven equipment. In addition, a coupling serves to protect costly equipment from the effects of misalignment, shock loads, vibration and shaft end float. Of these factors, the most common is misalignment and end float (also known as axial misalignment).
Misalignment is a condition created by two shafts whose axes are not in the same straight line. There are three forms of misalignment: parallel, angular, or the combination of the two. End float is the relative motion of two shaft ends.
Parallel misalignment occurs when the axes of the connected shafts are parallel, but not in the same straight line.
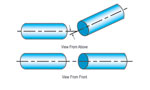
Angular misalignment occurs when the axes of the shafts intersect at the center point of the coupling.
End float (and Axial Misalignment) occurs when one shaft moves along it’s axis relative to the other shaft.
Misalignment can result from a combination of manufacturing tolerances, poor installation practices, thermal growth or shrinkage, foundation movement, and/or component wear. The combination of angular and parallel misalignment within a system may be more detrimental to the coupling and equipment than either of the individual misalignment.
Axial misalignment- result of either thrust loads, reaction loads, or heat generated movement – compounds the problem. Understanding the amount of misalignment that the coupling must handle or installing a coupling where it exceeds a maximum rated misalignment can result in premature coupling failure and/or significant equipment damage.