Variable Speed Drives
- Very economical and reliable method of speed change
- Allows the user to find the ideal speed without changing sheaves and belts; especially important on applications where final driven speed is critical and difficult to attain with two fixed-diameter sheave
- Speed range within the ratio is infinite, and speed change is accomplished quickly, while the drive is running
- Can be used as a highly efficient belt tensioner, with no adjustment necessary
- Offers a form of “soft start,” eliminating belt slip and premature wear
- On belt drives with inherent high torque start-up requirements
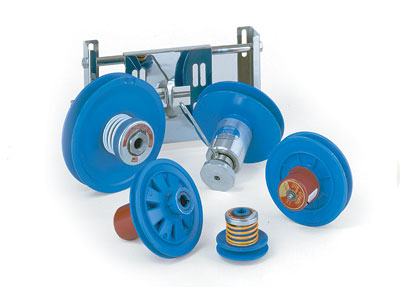
Resources
Variable Speed Drives Product Information
Why Vary Speed?
Variable speed drives are needed because many applications are not run at the same speed all of the time, due to the surrounding conditions. Revolutions per minute (RPM) of the driven shaft need to be increased or decreased when there are changes in load conditions, application requirements, or other circumstances.
Variable speed belt drives achieve the versatility needed to maximize application efficiency and productivity while remaining an inexpensive solution. In the most typical installation, a belt connects a variable speed pulley to a driven sheave. The pulley is mounted on a motor shaft and the motor is at constant speed. Thus, the speed at the driven shaft is a ratio of the pitch diameters of the pulley and sheave.
Please download catalog for sizing instructions and dimensional data. Please note, Lovejoy no longer provides belts.